Expert Tips on Implementing Foam Control in Chemical Handling Environments
Expert Tips on Implementing Foam Control in Chemical Handling Environments
Blog Article
The Role of Foam Control in Enhancing Product Quality and Efficiency
Foam control is an often-overlooked yet important component in the pursuit of item top quality and operational efficiency across varied sectors. By properly handling foam formation, companies can not only boost the uniformity of their formulas but also deal with operational challenges that can impede performance. This conversation will certainly explore the multifaceted effect of foam on both item stability and production processes, elevating crucial concerns concerning the techniques that can be employed to maximize foam control. As we think about these implications, it comes to be clear that the stakes are more than they could originally appear.
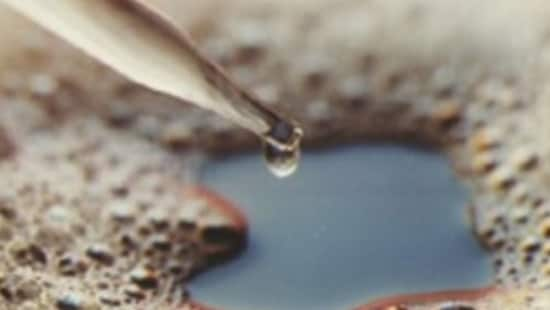
Recognizing Foam Formation
Foam development is a complicated sensation that can considerably influence product top quality and operational efficiency throughout various markets. Recognizing these variables is important for taking care of foam efficiently.
The liquid's thickness and surface tension play essential duties in foam stability. Surfactants, for example, can lower surface area tension, promoting bubble development yet also improving foam security, which can be bothersome in particular applications. Mechanical frustration, temperature fluctuations, and the existence of pollutants can worsen foam generation, making it crucial to monitor these facets during production processes.
Industries such as food and beverage, pharmaceuticals, and chemical manufacturing must be especially cautious regarding foam control. By grasping the underlying mechanisms of foam formation, companies can apply targeted approaches to minimize its results, therefore maintaining functional effectiveness and making sure constant product performance.
Impact on Product Quality
The visibility of foam can dramatically endanger item top quality throughout different industries. In making procedures such as food and beverage, drugs, and cosmetics, too much foam can cause inconsistent product solutions. As an example, in food production, foam may trap air, affecting appearance and taste, which can eventually alter customer understanding and contentment.
In addition, foam can impede the uniformity of layers and paints, causing flaws like bubbles and uneven coatings. In pharmaceutical applications, foam can disrupt the exact dosing of fluid medications, possibly affecting healing effectiveness and patient security. These quality problems not just diminish completion product's charm yet can likewise bring about costly recalls and damages to brand track record.
In addition, the presence of foam can make complex high quality control measures, making it tough to attain precise measurements and constant outcomes. Reliable foam control not only alleviates these risks but likewise boosts overall product top quality by ensuring that formulas satisfy rigorous market requirements. By purchasing foam control strategies, business can secure their items, enhance consumer satisfaction, and preserve an affordable side in the industry.
Functional Obstacles From Foam
Efficient procedures in various industries can be significantly interfered with by the visibility of foam, which poses multiple obstacles throughout manufacturing procedures. Foam can prevent blending and response times, impeding the efficiency of chemical procedures. In sectors such as food and drink, foam development can bring about imprecise fill this hyperlink degrees, causing item waste and inconsistencies in packaging.
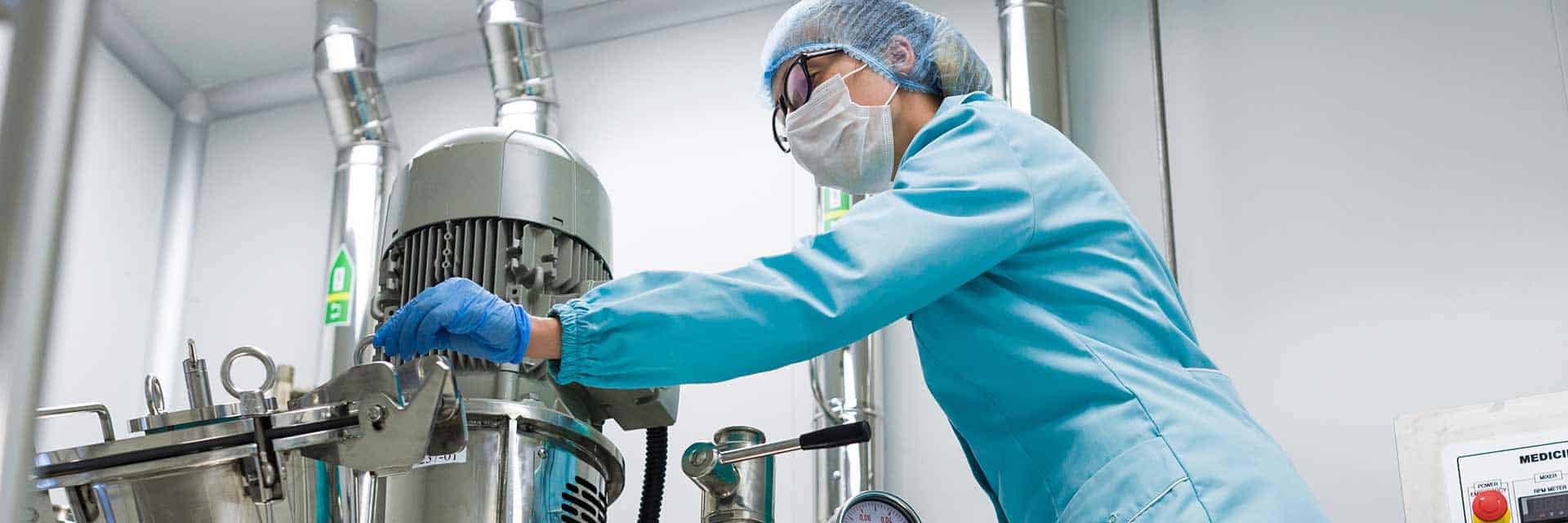
In settings where health is extremely important, such as drugs and food handling, foam can make complex cleansing methods, creating hidden reservoirs for contaminants. This not only increases quality problems however likewise can cause conformity concerns with regulatory standards.
Furthermore, the emotional effect on drivers can not be ignored; extreme foam can create a chaotic job setting, causing reduced morale and productivity. In recap, attending to the operational difficulties positioned by foam is crucial to maintaining performance and item top quality in different industries.
Strategies for Reliable Foam Control
How can sectors successfully reduce the obstacles presented by foam? Effective foam control approaches are vital for boosting product top quality and operational performance. One primary technique is the use of defoamers, which are chemical representatives designed to minimize or eliminate foam formation. Choosing the appropriate defoamer needs a thorough understanding of the particular procedure problems and the materials entailed.
Along with chemical options, procedure news optimization plays an important function in foam monitoring. Industries can assess and change specifications such as blending temperature, speed, and pressure to minimize foam generation. Executing devices adjustments, like mounting foam-breaking tools or adjusting container layout, can further help lower foam levels.
Regular monitoring and analysis of foam behavior within production processes are additionally vital. Making use of innovative sensing units and analytics can offer real-time information, enabling for prompt treatments and modifications. Personnel training is similarly essential; making sure that workers are experienced concerning foam characteristics and control methods can cause positive foam management.
Study and Sector Applications
While lots of markets deal with distinct challenges connected to foam control, study disclose that tailored techniques can substantially enhance both item top quality and operational efficiency. In the pharmaceutical field, for example, a leading maker executed a custom foam control approach that minimized foam formation throughout fermentation processes. This development not just enhanced yield by 15% yet likewise minimized contamination dangers, guaranteeing greater item honesty.
Likewise, in the food and drink market, a significant dairy products producer faced excessive foam during pasteurization - Foam Control. By introducing a specialized antifoam agent, they lowered processing time by 20%, which straight equated to raised throughput and decreased power consumption. The application of foam control gauges ensured consistent item texture and taste, enhancing brand commitment
In the chemical production market, a case research study highlighted the effective application of foam control in wastewater treatment processes. The execution of a real-time monitoring system enabled drivers to adjust antifoam dose dynamically, bring about a 30% reduction in chemical usage and boosted effluent quality.
These study highlight the diverse applications of foam control across sectors, emphasizing its vital duty in enhancing product quality and functional performance.
Conclusion
In final thought, reliable foam control is indispensable to enhancing product quality and operational effectiveness throughout numerous sectors. By addressing foam formation, companies can reduce the negative effects on formulas, appearance, and application precision. Applying targeted foam monitoring strategies not only decreases processing delays and waste but additionally reinforces tools dependability. Eventually, prioritizing foam control adds to improved productivity, protecting brand credibility, and increasing customer fulfillment, highlighting its relevance in quality control within manufacturing processes.
Foam control is an often-overlooked yet vital part in the quest of product high quality and operational performance across diverse markets. Staff training is just as crucial; guaranteeing that employees are well-informed about foam characteristics and control techniques can lead to positive this article foam management.
While several industries encounter one-of-a-kind challenges connected to foam control, situation studies expose that customized techniques can significantly improve both item high quality and functional efficiency (Foam Control). In the pharmaceutical market, for instance, a leading producer applied a custom-made foam control method that reduced foam development throughout fermentation processes.In final thought, reliable foam control is essential to improving item top quality and operational effectiveness throughout various markets
Report this page